Our
Processing Flow
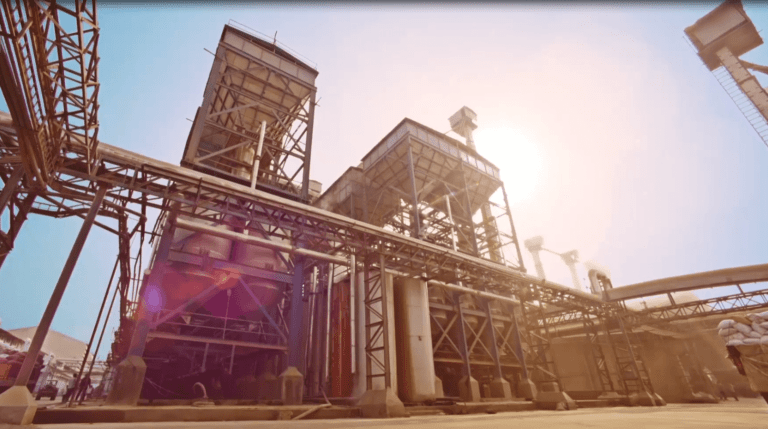
Steam Generation
The raw water obtain from the bore wells will be treated in reverse osmosis plant to remove scaling materials and other impurities. The treated water is fed into the boiler with the help of feed water pumps with high pressure. The rice husk is fed in to the boiler furnace through conveyor system. The heat generated in the furnace boils the water in the tubes to the required temperature and to produce steam. The high pressure (65kg/cm2 490o C) steam is then passed to the turbine for generation of power.
Power Generation
The high-pressure steam produced at the boiler will be fed in to the turbine. The turbine rotates with the help of the steam inducted into it and thus rotates the alternator to produce the required power. The turbine is a multistage and complete back pressure. The turbine supplies steam required for the other units of the complex at reduced pressure (1.5kg/cm2). The condensate water is again recirculated in to the boiler feed water tank for pumping in to the boiler again. The power generated at the turbo alternator is fed in to the transformer yard.
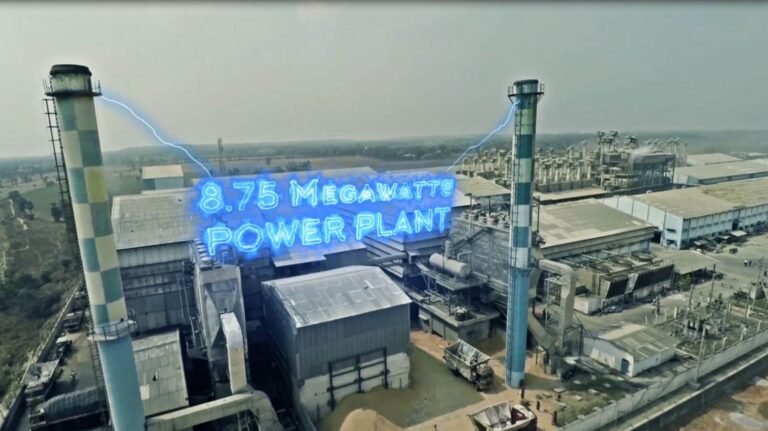

Power Transmission
The power generated at the turbo alternator is taken into the transformer for setup or step down of the voltage. From the transformer yard where several distribution and safety apparatuses are fixed, a power is sent to the local distribution system for the captive use.